The quality of packaging technical processes is one of the key criteria for product competitiveness. Correspondence of the actual volume to the declared one, hermetic capping and an even label have a significant impact on the overall impression of the consumer about the product. That is why responsible manufacturers carefully choose equipment, choosing in favor of reliable installations of reputable brands.
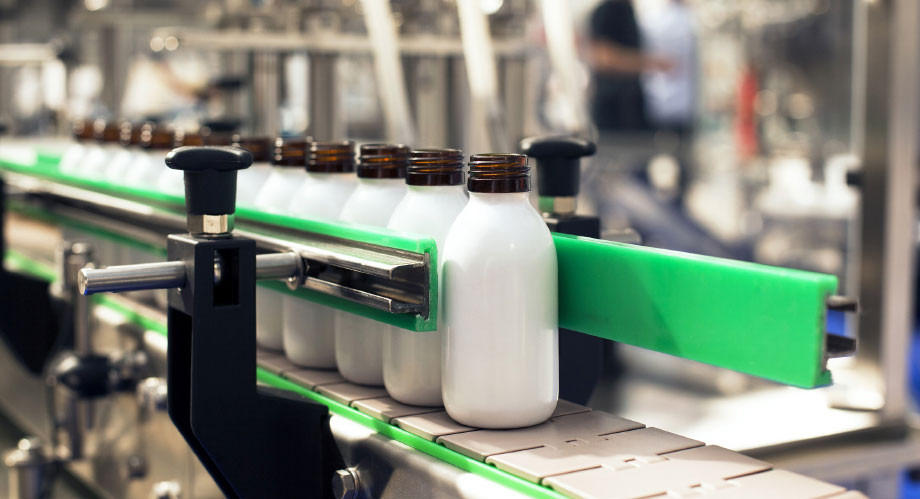
Of course, any machine, whether it is a dispenser, a sink, a capper, a labeler or a marking machine, cannot guarantee 100% accuracy. Errors of the installers and operators, improperly adjusted units and other similar factors can lead to poor-quality operation of individual sections of the installation and, as a consequence, to the occurrence of packaging defects. To avoid this, manufacturers organize final control areas where product quality is monitored and defective products are rejected. Enterprises that produce goods in small batches most often involve additional staff who, through inspection, weighing and other types of control, perform rejection. On high-performance packaging lines, quality control is carried out by special equipment - inspection machines.
How do inspection facilities work?
Machines using sensors and special measuring devices evaluate each unit of goods, process the data obtained and, based on the evaluation results, sort or reject products. Before starting work, the operator sets the parameters defining the defect criterion: permissible deviations by weight, a diagram of the position of the lid and a number of others. The inspection machine will automatically recognize a low-quality product in accordance with the specified algorithm. A product that does not meet production standards, will no longer reach the next technological section and will not be subjected to further operations. The advantages of equipping the line with an inspection installation are obvious - low-quality goods are promptly removed from the general flow, while the influence of the human factor is minimized.
What types of control do inspection machines carry out?
On today’s market, there is a wide variety of inspection systems for product quality control at every stage of packaging:
· Control of container cleanliness after washing;
· Control of empty containers for chips, cracks and other mechanical defects;
· Control of product loading level and dose accuracy;
· Monitoring the presence of foreign particles in the container;
· Control of tightness of capping;
· Monitoring the presence of attachments to the box (for example, leaflets);
· Verification of the labeling data.
Our solutions for product quality monitoring
Our company supplies highly intelligent product quality control systems that demonstrate precision accuracy and stability. Particularly noteworthy are the so-called checkweighers, which are in demand today. They are the machines for weight control and rejection. Automatic checkweighers, models MI-400VO and MVO-3000, are optimal for working in packaging areas of large batches of medicines, cosmetics, food products, household chemical goods. The installations are linear units with three-section slat conveyors. Weighing products is carried out using weigh cells. Data from the devices is processed by the analyzer, after which they are properly transmitted to the operator panel display. The machines are equipped with special pushers that unload low-quality products in a separate tray.
The advantage of our production inspection machines is ease of setup and ease of use. All models are equipped with PLC-based software modules and fault management systems. The equipment can be integrated into the production line or work autonomously. Checkweighers produced by AURORA PACK ENGINEERING can completely eliminate the production of defective products, reduce the workload on personnel and increase the overall productivity of the control site.