Introduction of the goods to the consumer begins with study of the label. Information about the composition, place of production, release date and other data about the product is placed on the label that adorns the package. Many people fear buying a product without a label: it is too likely to become the owner of a low-quality fake. Responsible manufacturers ensure that product data is fully accessible to customers and help them make informed choices.
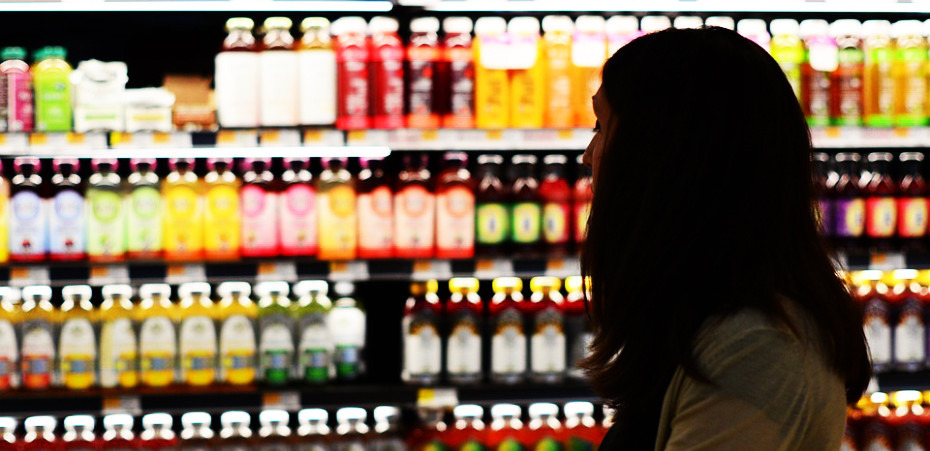
For the label to become not only an information field, but also a decoration of the package, it must be placed evenly and neatly, without folds and with tightly smoothed edges. Labeling machines are used to achieve the best quality of this process. In this article, we will focus on such machines: we will write about their types, features and advantages that will help greatly facilitate the search for suitable equipment. The importance of the right choice in this case is undeniable, because the result of the application will directly affect the appearance of the product, and the presentability of the package, as you know, forms the corresponding idea of its contents.
What are labeling machines and what functions do they perform?
Labeling machine is a specialized equipment for labeling containers. Complexes of this type realize the full cycle of processes: feeding and unloading containers, labeling and rolling over the label, and some models carry out preliminary drying of containers, date stamping and a number of other operations.
The application of any label (self-adhesive, heat-shrinkable, adhesive) has a number of its own peculiarities, which is why today in the packaging equipment market labeling machines presented in a wide variety. In accordance with the capabilities of a particular model, the equipment can work with different-sized containers made of plastic, glass, cardboard and other materials and apply labels to vials, bottles, cans, glasses, containers, tubes, syringes, ampoules and other containers.
The importance of such units is invaluable, since labeling is a rather labor-intensive technological process. For smooth application, it is necessary to pre-center the label, having verified all the necessary distances relative to the surface of the container, since after gluing it will be impossible to adjust its position. Automatic labelers manage this task efficiently and quickly.
Varieties and features of automatic labelers
Depending on the method of moving containers between sections, labeling complexes are divided into carousel and linear types of machines. Both types belong to the category of high-performance equipment and are used mainly at large industrial enterprises. Within an hour of operation, such units label from 4000 to 10000 containers.
Carousel-type (rotary) machines are equipped with a rotary table, which moves the bottles in a circle, with the alternate transition from one position to the next. In linear machines, a conveyor transports containers. The type of conveyor (linear or plate) is determined based on the characteristics of the container, and the length and presence of rotary sections depend on the configuration of the entire packaging line. The advantages of these machines are the modularity of the design, which makes it easy and quick to replace individual elements or complement the installation with additional devices.
One of the key factors in choosing the right equipment is the ability to implement a specific labeling technology. Each manufacturer decides how to arrange the packaging and where to place the label, and each labeling complex is made considering this need. The label can be applied only to one or several sides of the container, which is often found on vials and bottles with alcoholic beverages, cosmetic creams, shampoos, and cleaning products. Circular labeling involves placing 360o on the entire surface of the container and is most in demand by enterprises producing soft drinks, milk, kefir, canned food, pharmaceutical and veterinary preparations. Often we see goods with labels applied only on the lids (for example, cans with canned vegetables, fruits, juices, pickled mushrooms, as well as buckets with paint and varnish products).
A number of installations are equipped with universal elements (applicators and other devices) that allow you to work effectively with different types of containers: round, cylindrical, square and other shapes. This is especially true for companies practicing frequent rebranding of packaging. Some models demonstrate a combined approach by sticking coils, front and rear labels in one cycle of work.
Design and equipment of labeling complexes
The labeling machine can be used as a stand-alone machine with a fully autonomous control system. However, in recent years, more and more companies have chosen complete lines to equip production, where immediately or later (during modernization) the labeler is integrated. In this case, the setting and regulation of operation parameters is carried out using a common PLC panel with a touch screen. Regardless of the chosen method of operation (independent or as part of a line) only one operator is required as maintenance personnel. The level of specialist training does not matter, since such an interface is mastered, as a rule, easily and quickly.
The continuity of processes in such complexes is carried out by equipping with intellectual functions. For example, the option “no bottle - no labeling” is implemented due to special sensors that stop the machine in the absence of containers or untimely replacement of the roll with labels. This, in turn, avoids packaging defects. In addition, in most models automatic speed control is provided in accordance with the flow volume of incoming containers.
The functionality of the labeling machines is limited only by the budget and the requirements of the Customer. Large manufacturers can make the installation with any individual equipment. Therefore, machines are often supplemented by thermal transfer or ink jet printers for printing the date, batch number and other marking data. When using fragile, light or unstable containers, the upper clamping conveyor is installed, which ensures its correct positioning while moving along the conveyor and eliminates tipping or deformation.
Progressive management systems that underpin the operation of modern labeling systems can be synchronized with accounting programs to effectively track information about the quantity of goods produced. This option greatly facilitates management of product accounting processes and audits.